Districts across the country are making the switch to electric. Here’s what they’ve learned.
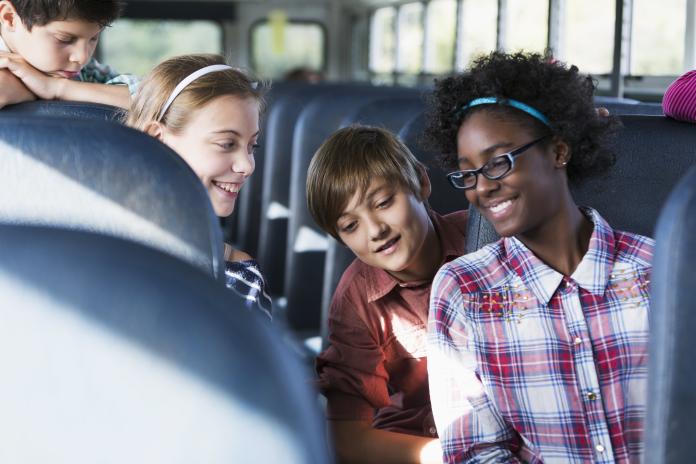
Electric school buses are heading to communities across the country. As of December 2022, school districts and fleet operators in all 50 states have committed to electric school buses – for a total of 5,612 electric school buses that are on the road or will be in the coming years.
Here are a dozen tips gathered from school districts who have already started the electrification journey. For even more information, please check out our individual stories from school districts across the country that have gone electric.
Note: If your school district contracts out for school transportation services, your contractor will likely be responsible for many of the elements listed below. Still, it is important for school districts to understand their electrification needs and goals to make informed contracting decisions.
Foundation Setting
1. Designate a project manager responsible for guiding electrification efforts and convening appropriate stakeholders and decision makers
Why: Adopting electric school buses, whether one bus or a full fleet conversion, is an achievable yet complex project. As such, specifying a staff member responsible for shepherding and coordinating the project is critical to ensuring its success.
To adopt electric school buses, school districts will need to coordinate with a variety of stakeholders, install new infrastructure and train staff. These elements typically span multiple school district departments, as well as other offices and agencies. With a designated staff member leading the project, school districts have been able to avoid delays, improve communication and mitigate other challenges that may limit the project’s timeliness and success. Designating a Project Manager in California’s Stockton Unified School District and Modesto City Schools, for example, improved the experience of managing project streams, writing grants, creating fleet transition plans and designs, and tracking and analyzing data for reporting purposes.
The Project Manager can convene all key stakeholders, including community members and decision-makers, and create alignment early in the planning process. They could be a Business Manager, a Sustainability Manager, an Energy Manager, a Transportation Director, a new hire or another party. The Project Manager can ensure that drivers, mechanics and operations staff – those who will engage with the electric school buses firsthand – are part of the process and that their concerns are understood and addressed. Coordination with an accounting department or business team will be important for funding applications; product orders for buses, chargers and software; and (if applicable) requests for information (RFI) or requests for proposal (RFP), among other considerations. Additionally, a Project Manager or team may look externally for support by hiring consulting firms or securing pro-bono support (reach out to the ESB Initiative for one-on-one sessions here).
2. Partner with local groups to build momentum
Why: Advocacy groups can be a powerful partner in building momentum and often represent those experiencing the worst effects of vehicle pollution. Working with communities from the start can lead to more successful project implementation. Groups with an equity focus can help provide important input and perspective on addressing the needs of underserved communities.
Examples include Chispa Arizona, who worked with mothers and other community members on the passage of a school bond that would help underwrite Cartwright Elementary School District’s (and Arizona’s) first electric school bus; and Mothers Out Front Virginia, who put pressure on Fairfax County’s school board to set a carbon neutral goal that resulted in a commitment to fully transition their fleet of 1,625 buses to electric or zero-carbon alternatives by 2035. Students, as seen in Miami, can also be powerful advocates for their own future.
3. Engage communities early in planning and advance an equitable approach to electrification
Why: Students, parents and caregivers, school district employees, communities located near depots, maintenance workers and other workers in the electric school bus supply chain all have a stake in the project and relevant expertise to contribute.
Engaging communities with on-the-ground expertise, particularly groups and individuals that have been historically excluded from planning processes, can improve projects by uncovering barriers and blind spots early in the process. Meaningful and consistent community engagement can also improve project buy-in and long-term sustainability. While some of the most empowering forms of community engagement enable communities to co-create projects, working with communities throughout the planning and implementation phases builds trust, increases investment and produces creative solutions. In California’s Clean Mobility in Schools project, one school district is looking to The Greenlining Institute’s Mobility Equity Framework to inform how to center equity in the mission, process and operations of its electric school bus effort, while another district subcontracted with a local nonprofit for community outreach and engagement strategies.
The first step for community engagement requires identifying the key communities and building trust with them. As you build these relationships, you can work together to identify the most effective mechanisms for engagement. Some groups will be more receptive to short surveys and online engagement, while others may value one-on-one conversations or being in the room during the planning process. It is helpful to consider how to enable broad participation by holding forums virtually or in locations convenient to transportation and at a variety of times to accommodate various work schedules. Regardless of the community, consistent follow-up to share results and explain how their input impacts the project is important.
Charging Infrastructure and Operations Planning
4. Establish contact immediately with your electric utility on infrastructure planning to install now and plan for the future
Why: Building out charging infrastructure can take one week to 24 months depending on project complexity and power needs, so planning with your electric utility should be one of your first steps as soon as you begin considering electric school buses for your fleet.
With proper planning and engagement, interactions with your power provider can be more productive, saving time in the electric utility connection process. If connecting new service is necessary — which will likely be the case for more than six Level 2 chargers or one Direct Current (DC) fast charger — this could take 12-18 months. For larger transitions, you may consider hiring an engineering, procurement and construction (EPC) firm to facilitate gathering the necessary site information or hiring a consultant or contractor to analyze your short-term and long-term acquisition strategy.
A focus on longer-term planning by integrating “future proofing” (see photos below) electrical installations can minimize site disturbances and rework, resulting in cost savings for school districts. For example, in Beaverton, Oregon, the school district built out electrical capacity to support eight buses although it had only received two buses upon construction completion. Regardless of the charger make, model or design, the power connections they installed can meet some future needs. They were also able to avoid expensive trenching by placing conduit along an existing wall.
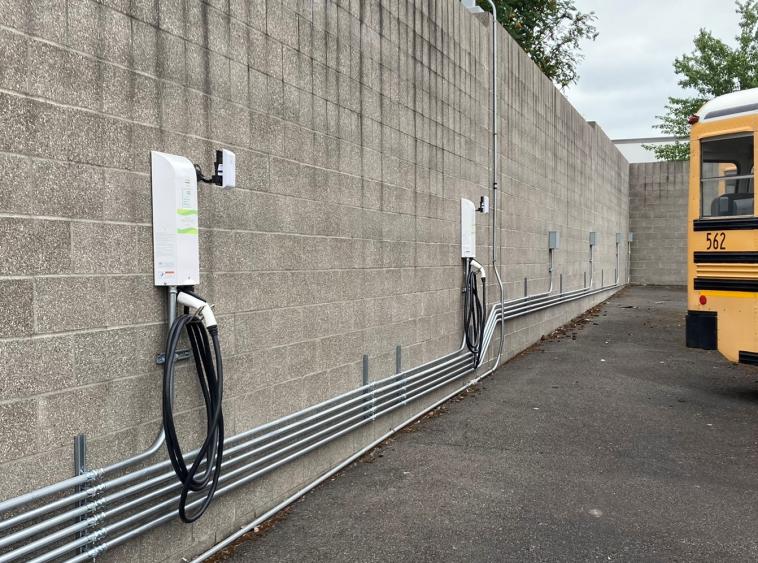
Your electric utility may offer electric vehicle-specific charging rates or rebate opportunities, or cover a portion of utility-side costs (e.g., make-ready programs, transformer, or other upgrade costs). This resource offers a list of questions to ask your electric utility, and these videos are designed to help you better understand site considerations.
5. Understand additional coordination that may be needed at leased depots
Why: If a school bus operator leases land for its sites, landlord coordination may slow down the process of upgrading a site.
Identifying the impacts of this dynamic early on can help mitigate delays related to:
- Complexity in identifying key accounts manager: Electric utilities are required to protect sensitive customer information, or personally identifiable information (PII), by law. By sending over your meter number(s) to your electric utility, they can let you know who will need to approve access to data like historic electricity bill components.
- Landlord authorization: Your electric utility may require a letter of authorization from your landlord in order to start charging infrastructure planning.
- Legal considerations: Coordinating with attorneys or legal professionals may be necessary. Adding a clause to lease agreements pertaining to ownership of infrastructure may help minimize risk.
Procurement and Installation
6. Negotiate workforce training provisions in contracts or purchase orders to build internal capacity
Why: Without explicitly stating and contractually obligating a robust training program and resources from the OEM (Original Equipment Manufacturer) or dealer for both drivers and mechanics, the OEM may not anticipate the level of training you require.
Electric school buses contain several basic vehicle systems also found on a diesel bus (braking, steering, tires, windshield wipers, lights, etc.) that require the same preventative maintenance and upkeep. Electric school buses also contain many new systems and components that maintenance techs must receive new training on before they are able to safely and successfully troubleshoot and resolve issues that may arise.
Stipulating in bus purchase contracts or requests for proposals (RFPs) that the manufacturer and/or dealer provide robust electric school bus maintenance training can support internal workforce capabilities. For example, Twin Rivers Unified School District in California operates 50 electric Type A, C, and D buses. Twin Rivers’ vehicle maintenance manager notes (Page 8 of report) that effectively training on-site technicians to troubleshoot and address a wider range of issues can reduce downtime by solving simple issues internally. Asking specific questions about how many hours of support are included with your purchase and getting quotes for additional training available are best practices.
7. Ensure compatibility of various system components
Why: Compatibility issues can result between buses, software, chargers, utility-side infrastructure, or other elements. Confirming that all your elements can “talk to one another” can help avoid unexpected costs or delays.
Coordinate early with your manufacturer or dealer to make sure the buses, chargers, and software management platforms you plan to install are all compatible. Currently, most electric school buses are configured to work with specific chargers. These chargers may only work with one type of electric school bus or electric vehicle, so it is very important to engage your electric school bus manufacturer, charger manufacturer and network/software provider early on to make sure the bus is compatible with the charger you are installing. Some buses may have a maximum power level they can receive from a charger, and “right-sizing” chargers to fit your needs (like buying a lower power level charger) may help save money, as Salt Lake City School District discovered. A network/software provider can also manage your charger to meet electric school bus charging requirements.
Alert your electric utility if you plan to integrate chargers with different system requirements, like in the case of the Eastern Band of Cherokee Indians where different chargers (which were necessary to fulfil the requirements of two different funding streams) required different conduit. Reaching out to other school districts that are using the products you are considering can offer insights into operational issues and help avoid pitfalls.
8. Utilize managed charging to improve user experience and save money
Why: Successful remote operation of chargers through managed charging can help charge when electricity rates are lowest, minimize the need to manually move cables during charging sessions, and send notifications of any issues or interruptions during a charging session.
Consider selecting a “smart” or managed charger that offers remote operation of the chargers once plugged in, including troubleshooting and real time management of energy consumption. One step further would be to work with a third-party subscription service to integrate a “networked” charging solution that manages the operation of multiple chargers on your behalf. While chargers equipped with managed charging may be more expensive and have a monthly or annual subscription rate, a 2015–18 electric school bus pilot at three Massachusetts school districts found that unmanaged bus charging and high parasitic loads (e.g., bus heaters, fans, lights) during charging contributed to electricity costs being 63% higher than necessary. To avoid excess energy consumption, the report's authors recommended managed charging. See the All About Managed Charging and “Vehicle-to-Everything” or V2X page for more information.
Training, Testing and Deployment
9. Train drivers to adopt behaviors that increase range and efficiency
Why: Smooth driving and the use of regenerative braking can impact bus efficiency.
Leveraging regenerative braking can simultaneously lower wear on braking systems and capture energy to extend the range of the bus in route. This style of “one-foot” driving is new to operators and requires practice; telematics can help capture driving efficiency, and one Canadian school district has included it in its driver trainings. Bus dealers or suppliers may include a training(s) in their package. According to Salt Lake City, the "sweet spot" for regenerative braking is about 55 miles per gallon — at higher speeds the regenerative braking will turn off for safety purposes, with the exact threshold dependent on the model.
10. Work with first responders
Why: While electric school buses are designed to the highest safety specifications, first responders need to be educated on proper management of electric powertrain and battery configurations.
Allowing first responders to become familiar with an electric vehicle’s unique features and identify best practices will help ensure effective emergency responses and confidence for first responders. School districts can conduct safety trainings to help first responders better understand battery configurations, including identifying manual battery disconnect switch locations inside and outside of the bus, as well as proper ways to tow an electric school bus. Sometimes bus dealers or suppliers can help with this training as well.
Performance, Benefits and Scaling
11. Include a plan for monitoring
Why: For large scale transitions, maintaining metrics can shed light on deployment progress and keep stakeholder groups involved.
Before electric buses arrive, work with stakeholders, including community members, to identify indicators of success and how to track them. These could include: number of electric miles driven; bus up-time percent; percent of drivers, mechanics, and technicians fully trained; number of routes in high pollution corridors; number of community members meaningfully engaged (by group or individually); fuel and energy cost reductions; and greenhouse gas or other air pollutants avoided. For example, Knox County, Missouri, tracks their performance publicly on an online dashboard. Districts can also provide students with a hands-on science project by having them set up air quality monitors to see the difference for themselves.
12. Get creative on student engagement
Why: Electric school bus benefits for students extend beyond air quality improvements and a smoother ride when the topic is integrated into Science, Technology, Engineering, the Arts, and Mathematics (STEAM) curricula.
School districts are getting creative with how electric school buses can bolster students’ learning experiences:
- In Knox County, Missouri, the school district turned an old diesel bus into a coffee shop that offers learning opportunities for industrial tech, business, media, and agriculture students.
- In Cherokee, North Carolina, the Eastern Band of Cherokee Indians’ Air Quality Program taught a 5th grade class the benefits of their electric school bus. These fifth graders, in turn, presented the information to a class of pre-kindergarten students.
- In Stockton, California, the school district’s student-led Energy Patrol aims to educate teachers and students on energy efficiency and cost saving actions (videos in English and Spanish).