How Electric School Bus Fleet Owners Can Ensure That Their Used Vehicle Batteries Avoid the Landfill – and Reap Economic and Environmental Benefits
For school districts and other electric school bus fleet owners, gaining value from used vehicle batteries starts during procurement.
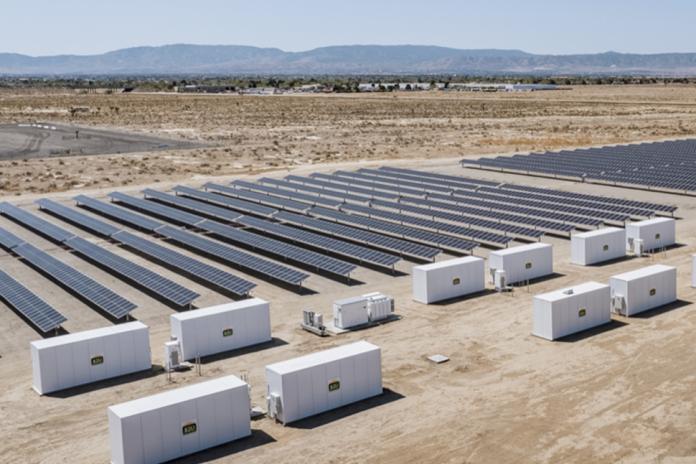
Introduction
With billions of dollars in funding and incentives available for electric school buses (ESBs) and charging infrastructure, ESB adoption is set to skyrocket. This means a comparable increase in the number of ESB batteries in circulation – about 480,000 under the first round of full fleet electrification. As these batteries are used, their performance and capacity to hold energy degrade over time. At a certain point, typically after 8-10 years, they can no longer function as a school bus battery due to degradation over time, but they usually retain some storage capacity. When these batteries reach their end of life (EOL) in the bus, they must be removed, replaced by a new battery and processed by trained personnel.
Without a responsible EOL management plan, the batteries may end up in a landfill, leaching toxic chemicals which contaminate the soil and water. Landfills can also leak gases, causing respiratory issues in the surrounding community. Since landfills are disproportionately sited in communities of color, those communities bear an inequitable portion of the negative impacts. This is in addition to the existing environmental and social harms borne by developing countries caused by extraction to make the battery in the first place.
Over time and use, batteries will degrade and lose capacity, which reduces the bus range. Usually, batteries will be replaced from ESBs when it still has around 70% remaining useful capacity (although lower capacity batteries can possibly still be used for shorter bus routes). Additionally, metals that make up ESB batteries can be recycled to make new batteries and reduce extraction. This value can be captured through circular practices that include three options: (1) second-life use, (2) refurbishing, or (3) recycling. This is called a closed loop value chain, which aims to minimize waste by developing economic value (and environmental benefits) at various stages after EOL. Proper end-of-life planning and management is important to ensure these outcomes and avoid the negative economic, environmental and social harms that would come from the used ESB batteries ending up in landfills.
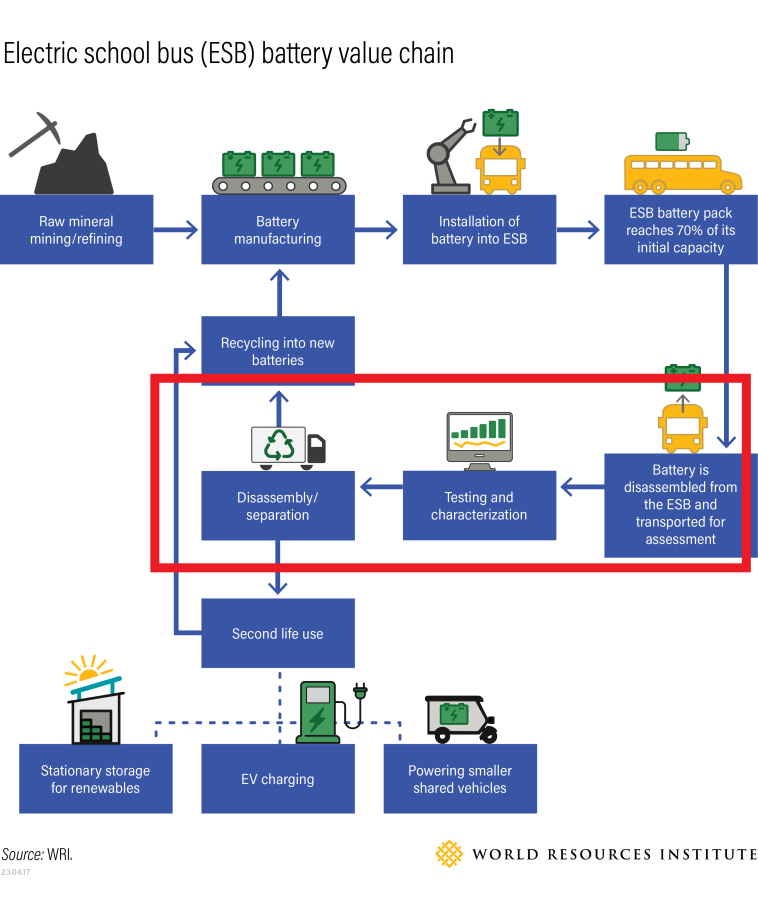
EOL battery management is complicated by the variability of bus and battery ownership models, which can involve school districts, contractors, utilities and other third parties. This article outlines how school districts, bus contractors and other EOL battery owners can support a closed loop ESB battery value chain by focusing on the activities in the red box in Figure 1. It provides a high-level overview of battery EOL options, the scenarios that fleet owners may encounter in this process, and the key stakeholders involved in the process. It concludes with recommendations on how to bolster sustainable EOL battery management via procurement, policy and partnership.
Options for battery end of life
Second-life use
A popular second-life application for used bus batteries is stationary storage. Some technologies allow for simply plugging a used battery into a storage system, while others involve disassembling and reassembling the battery into a pack specifically for use in stationary storage. Second-life use is also known as repurposing.
To minimize costs and maximize material utility, second-life use should be prioritized over recycling for ESB batteries. At the scale of the US school bus fleet, second-life use value is significant: there are approximately 480,000 school buses, and assuming an average ESB battery size of 150 kWh and 70% remaining capacity when removed from the bus, the remaining capacity for second-life use can be 50.4 GWh, equivalent to the average monthly electricity demand of over 56000 U.S. homes in 2022. The dominant battery chemistry for ESBs is Lithium-Iron-Phosphate (LFP), which are particularly long-lasting, safe and well-suited for energy storage. Although cost estimates for EOL processing vary (see cost table below), selling or leasing EOL batteries to second-life battery companies enables battery owners to generate additional revenue and reduce the total cost of ownership for their ESB fleet. As more companies and used battery volumes grow, second-life economics should solidify over time.
Refurbishing
Refurbishing is the emerging process of replacing some, but not all, of the components of a battery, enabling it to be used again in an ESB. Refurbishing is a good option for batteries that have experienced minor degradation (e.g. vehicle recalls, minor accidents), and common techniques include replacing the electrolyte solution, worn parts and / or nonfunctioning cells. Most companies that refurbish also recycle and can assess which option is appropriate for a particular battery.
Recycling
Recycling breaks down batteries into their component materials (e.g. plastics, metals and minerals) and processes them to manufacture new batteries. Battery recycling economics currently hinge on the quantity of valuable nickel and cobalt in a battery. Although the LFP chemistry common to ESB batteries does not contain these materials (a key reason why recycling LFP batteries is not economical today), the second most common ESB battery chemistry, Nickel Manganese Cobalt (NMC), has them in significant quantity (and thus can be economically recycled). The market for lithium-ion recycling first emerged to address consumer electronics batteries, and organizations like the ReCell Center are focused on advancing R&D and scaling efforts to improve battery recycling economics.
Thanks to tax credits in the Inflation Reduction Act, batteries containing domestically recycled materials can qualify for savings of up to 35% over batteries made using mined minerals. According to Argonne National Laboratory's EverBatt model, using recycled battery materials in new batteries lowers the environmental impacts of battery manufacturing, reducing life cycle greenhouse gas (GHG) emissions by up to 40%, water use by up to 50%, and energy use by up to 40%. Critically, using recycled materials in battery manufacturing avoids the significant human rights and health concerns associated with mineral mining.
Landfill
The EOL outcome we want to avoid is batteries being sent to hazardous waste landfills. In this case, used battery materials and their remaining value are lost. Because batteries do not decompose, landfilling risks toxic and reactive battery chemicals leeching into the surrounding environment and triggering landfill fires.
For an in-depth look at battery end of life options, see our article on electric school bus battery sustainability: How to Ensure a Sustainable Future for Electric School Bus Batteries.
Cost considerations
There are a variety of costs involved in battery end of life management, some of which may be the responsibility of the battery owner (school district, contractor, etc.):
- Dismantling: Batteries must be removed from the bus by personnel specially trained in electric vehicles battery dismantling and high voltage safety. It also requires specialized equipment.
- Battery testing: Used batteries must undergo testing to determine their state of health, i.e. degree of degradation and remaining capacity, which helps determine the ideal EOL pathway. Traditional testing methods are time intensive and require costly specialized equipment and personnel. Because of the variety of battery chemistries and manufacturers, there is a lack of testing standardization, making accurate valuation more difficult. Batteries with a better state of health and high remaining capacity will have a higher residual value when sold to a second-life use company. Companies like ReJoule are developing new methods of accurate and affordable battery testing compared to current solutions.
- Transportation: Used batteries are classified as hazardous waste after they are removed from the vehicle. The transportation of hazardous waste is governed by strict regulations by the U.S. Department of Transportation, including regulation on packaging. Depending on the distance, transportation can be one of the most expensive parts of battery EOL management. There are two ways used battery transportation are typically managed: 1) The fleet owner bears the cost, takes care of the logistics, and, with the help of trained dismantlers, drops off the battery at a predetermined site, or 2) The battery EOL company provides the transportation service and offsets the cost in the payout to the fleet owner for the residual value of the battery.
- Hazardous waste fee: Because of the increased risk posed by hazardous waste, those wishing to send it to a landfill must pay a fee. While landfilling could have the lowest out-of-pocket cost for the fleet owner, the true cost of landfilling to society is much higher when environmental degradation and restoration, public health impacts and future cleanup is considered. In contrast, second-life use is a revenue generating opportunity for school districts and must be prioritized instead.
Depending on the battery warranty, procurement contract and / or partnership agreements, school districts may be responsible for covering costs associated with transporting, dismantling, testing and selling their used batteries. Table 1 below shows various prices that school districts can expect to pay (or receive) for their used batteries.
Table 1: Price estimates for battery end of life processing
EOL Process | Cost | For a 150 kWh ESB battery |
Transportation of Used Batteries | $0.06 / nameplate kWh / mile (a) | $900 (f) |
Dismantling of Used Batteries | $1 - $5 / nameplate kWh (b) | $150 - $750 |
Testing of Used Batteries | $2 - $10 / nameplate kWh (c) | $300 - $1,500 |
Sales price of Used EV Battery | $19 - $131 / nameplate kWh (d) | $2,850 - $19,650 |
Hazardous Waste Landfill Fee | $80 - $140 / ton (e) | $80 - $140 (g) |
See citations for cells labeled a-g in the endnote to this article.
Three illustrative scenarios
Logistics pathways for EOL batteries is nascent but is the source for much confusion and uncertainty. The three scenarios below detail the most likely circumstances in which an ESB battery can reach EOL, each with different implications for responsible parties. These scenarios were developed through a series of conversations with battery second-life and recycling companies, dealers, school districts and vehicle manufacturers and are subject to change based on policy and technology developments.
Scenario 1: Replacement of the battery mid-bus life while under warranty
The battery reaches the end of its life as a bus battery during the bus’s lifetime, while the battery is still under warranty. In this scenario, the battery would be replaced by the dealer or designated service center, and the cost would be covered under the warranty. The dealer or service center would then be responsible for battery testing and determining what happens to the battery after it is removed from the bus. During procurement, it is important for fleet owners to establish level of service or support with the dealer or service center. Please see this easily modifiable Request for Proposal (RFP) template language that can be used.
After the battery has been removed, the dealer or service center can test the battery or bring in a third party to test the battery to determine the best course of action.
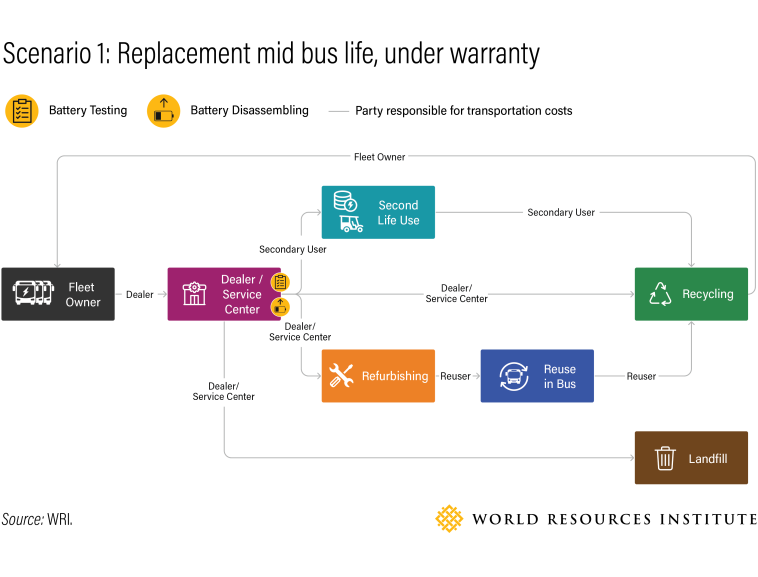
Scenario 2: Replacement of the battery mid-bus life, no longer under warranty
The battery reaches the end of its life as a bus battery during the bus’s lifetime, but the battery warranty has expired. This scenario is almost identical to scenario 1, except that the cost of replacing the battery would fall on the fleet owner. This includes the cost of labor to dismantle the battery (see Table 1), the cost of the new battery ($151 / kWh at the pack level in 2022), and the cost of disposing of the old battery (see Table 1). Battery disposal can either be handled by the fleet owner or by the dealer or service center that replaced the battery. In the second case, the cost of battery disposal would likely be included in the fee charged to the fleet owner for battery replacement.
In some cases, the fleet owner may choose to keep the battery to use for second-life use (which would still require engaging with a second-life use company). In this situation there will also likely be costs for battery dismantling and testing to ensure the battery is suited to the secondary application.
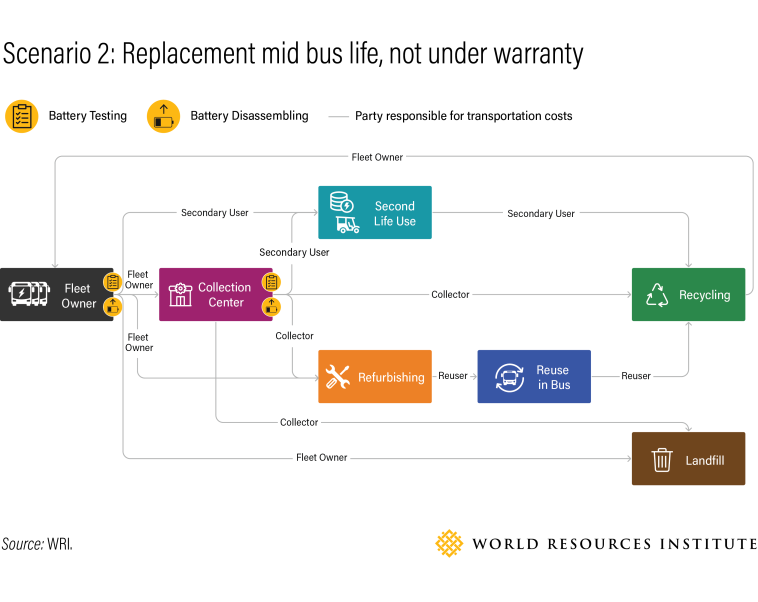
Scenario 3: End of bus life but replaced battery is still useful
In this scenario, the bus has reached the end of its life for school district service. The battery may still be in good enough condition to run a bus, but the bus it powered will have noticeably less range and poor battery health. In this scenario, the fleet owner will typically choose to sell the bus (including the battery) at auction.
The fleet owner may also choose to keep the battery for use in other applications. The downside of this approach is that electric buses without batteries are less valuable and more difficult to sell. In this case, the fleet owner would incur costs associated with battery dismantling and testing.
If the battery is owned by a third party, such as a power utility, fleet owners should consult with the third party on what to do with the battery when the bus has reached the end of its life.
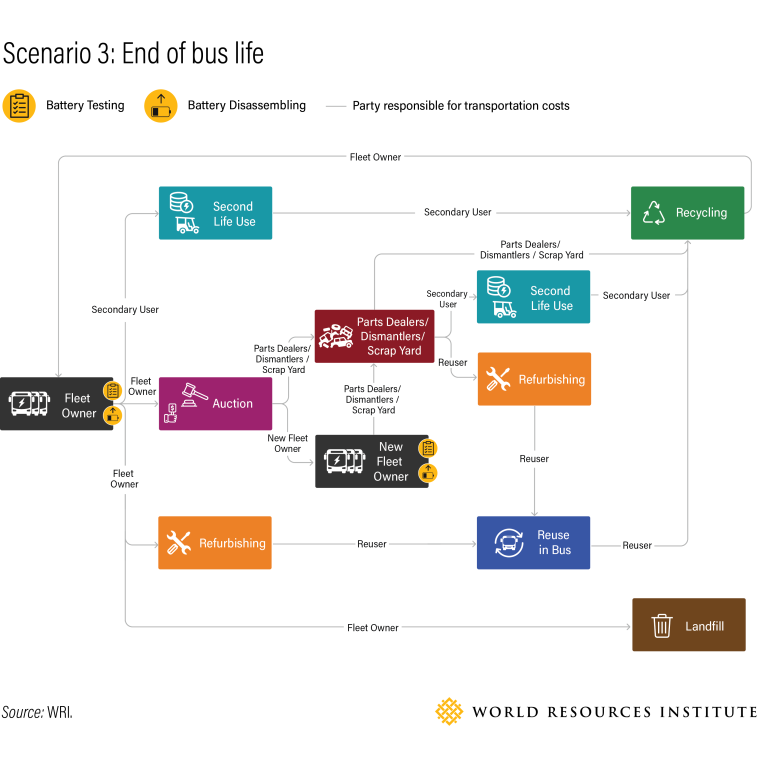
Recommendations
School Districts: EOL management starts during procurement
Although battery EOL may seem like an issue to be resolved years after receiving an ESB, school districts should clarify responsibilities during bus procurement to avoid surprises down the road. With ESBs making up just 1% of all school buses, the vast majority of ESBs are yet to be procured. Most school districts will be undertaking procurement over the next few years of their fleet transition. School districts should include the following considerations in the contract with their dealer or original equipment/vehicle manufacturer (OEM). However, districts with large fleets can consider contracting directly with second-life or recycling companies. The following dimensions should be covered:
- Battery warranty terms.
- Battery repurposing and/or recycling plans and processes at end of life, including partnerships, data sharing and revenue estimates.
- Battery replacement and decommissioning processes, including any costs associated with removal, handling, testing, transportation and assessments for battery reuse and/or recycling or disposal at end-of-life in the ESB.
- Battery ownership options.
These requirements can be included in the Request for Proposal (RFP) when school districts solicit ESB bids. WRI’s RFP template can help school districts get started.
Policymakers and OEMs have a role to play as well.
Policymakers: Mandates within incentive programs
With ESB prices remaining 3 – 4 times more expensive than their fossil fuel counterparts, the need for purchase incentives to spur adoption is clear. There are nearly $9 billion in federal and state incentive programs aimed at bridging the cost gap. This is a window of opportunity to ensure school bus batteries are not landfilled. These programs could require a battery EOL management plan from the OEM as part of the funding application which would clarify roles of stakeholders involved, indicate costs/revenue for the school district and OEM partnerships with battery second-life use and recycling companies.
The complexity surrounding school bus battery EOL management and risk of landfilling can be resolved by mandating extended producer responsibility (EPR). EPR is a policy tool widely used in the U.S. and globally that makes producers responsible for the EOL management of their products. In the U.S. today, 33 states have EPR policy for products ranging from consumer batteries to packaging, carpets to paint. Globally, the largest EV markets have mandated EPR for EV batteries, including the European Union, India and China. An EPR policy will ensure that bus manufacturers take back used batteries, helping avoid landfills entirely. Other benefits include providing confidence to school districts of safe disposal, aggregating batteries in high volume for more economical second life, refurbishing and recycling, and potential price reductions for new bus batteries.
OEMs: Strategic Partnerships
OEMs can help reduce risk of landfilling batteries at EOL by developing partnerships with battery second life and recycling companies. These partnerships will offer certainty to school districts and other fleet owners regarding a pathway for their used batteries. It should also help inform how batteries can be designed in the manufacturing phase to ease dismantling, testing, repurposing and recycling. These partnerships can help vehicle manufacturers get ahead of any federal or state mandates for EV battery EOL management like California’s SB 615 and Washington’s SB 5144.
Conclusion
It’s important for electric school bus owners to consider the EOL of their ESB battery at the start of their ESB journey. As things stand, EOL school bus batteries could end up in landfills, contributing to pollution which disproportionately harms communities of color and low-income communities. Advanced planning not only helps avoid this, but also enables bus battery owners to realize the remaining value of their used batteries and lower their total cost of ownership. School districts should use the opportunity of ESB procurement, spurred by federal and state programs, to ensure they are not left footing the bill of battery EOL management. But they are not alone - ensuring bus batteries avoid landfills and are utilized to its fullest will require bold action from policymakers and electric school bus OEMs too.
Procurement provisions, policy mandates and strategic partnerships are critical to sustainable and safe management of ESB batteries at their EOL. This way ESBs will strengthen the domestic U.S. battery supply chain and can demonstrate leadership in the U.S. medium-heavy duty vehicle industry.
Table 1 Sources:
a: NREL Battery Second-Use Cost Calculator
b: 2023 Applied Energy Research
c: ReJoule (in combination with the used battery cost and dismantling numbers)
d: NREL (2015)
e: This is the range between low fee southern states like Louisiana and high fee western states like California and includes tipping fees at the landfill, as well as hazardous waste disposal and generator fees.
f: Assuming the battery is transported 100 miles within a single state. Hazardous waste in the US is regulated by the EPA, but regulatory requirements and fees differ by state.
g: Assuming a battery pack weight of 6kg / kWh from Argonne National Labs Everbatt model.