How Electric School Bus Owners Can Maximize Battery Performance by Limiting Aging
Electric school bus battery performance naturally degrades over time. Fortunately, there are best practices electric school bus operators can follow to maximize performance. Here's what to know.
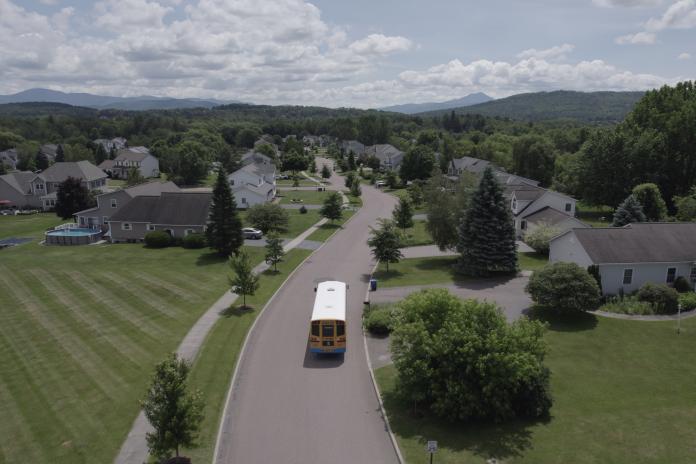
Lithium-ion batteries (LIBs) are incredibly useful for powering devices from smartphones to electric vehicles. Unfortunately, with time and use the lithium-ion batteries in Electric School Buses (ESBs) functionally degrade, just like those in your cell phone. This process is called battery “aging” or degradation, and it lowers battery capacity (the amount of energy the battery can store) and power (the rate the battery can accept or deliver energy). Fortunately for ESB owners, there are operational best practices to limit the speed of aging and maximize battery performance:
- Keep batteries in their optimal temperature range: 15 – 35°C (59 – 95°F). During operation this is accomplished by the battery thermal management system (standard in ESBs), but it is also helpful to control the environmental temperature during storage and charging.
- Use level 2 chargers (capping charging power at 19.2 kW) whenever possible and reserve fast charging for when limited downtime is available.
- Maintain a battery state of charge of 20 – 80% whenever possible.
To learn more about battery aging, the above best practices, and battery industry efforts to limit aging, keep reading!
How do Lithium-ion Batteries work?
To understand battery aging, it's important to first understand how LIBs work. The basic functionality of a LIB involves a reversible chemical reaction. When the battery is charging, lithium ions are released from the cathode (the positively charged electrode) and travel through the electrolyte and battery separator into the anode (the negatively charged electrode). At the same time, electrons are released from the cathode and sent to the anode, carrying the electrical charge that “charges” the battery. This reaction reverses as the battery is discharged: lithium ions and electrons are released from the anode and sent to the cathode. See the figure below.
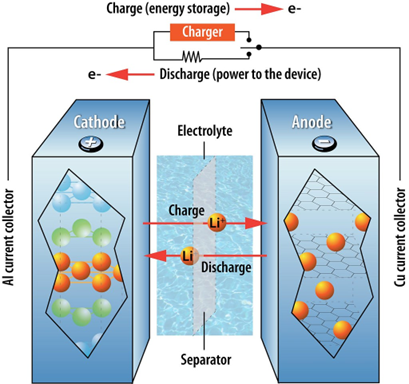
During the battery’s first charge cycle, the electrolyte solution reacts with the anode material forming a barrier called the solid electrolyte interface (SEI) that limits the rate of further reactions between the electrolyte and anode. Initially, the SEI is helpful, allowing lithium ions to pass through and the battery to charge and discharge, while slowing electrolyte and anode decomposition.
Unfortunately, battery chemistry is complicated and fragile, and a host of interrelated "aging mechanisms" cause battery capacity and power to drop with time and use. Battery capacity drops due to aging mechanisms which reduce the amount of lithium ions and electrode material in the battery, and battery power declines due to aging mechanisms which reduce the amount and electrical conductivity of electrode material. Although some level of aging is inevitable, it is possible to reduce the rate of advancement. The next section provides a high-level overview of the most common aging mechanisms and best practices for slowing them.
How does battery aging happen and how can it be deferred?
Aging Mechanism | Best Practice |
SEI Layer Growth Continued chemical reactions between the electrolyte and electrodes can cause the initially helpful anode SEI to grow too thick and generate an unhelpful cathode SEI layer. As these layers grow, fewer lithium ions can access the electrodes, lowering battery capacity and power. | Increasing temperature and voltage increases the likelihood of chemical reactions. Keeping batteries below 35°C (95°F) and storing them below 80% state of charge (SOC) helps to limit unwanted reactions. |
Lithium Plating When lithium ions arrive at the anode faster than they can enter into the material, the lithium can become permanently deposited on the anode’s surface. This is known as lithium plating, and it lowers the electrolyte’s lithium content and the amount of anode material available to store ions. As less anode is available to store ions, the rate of lithium plating accelerates over time causing the formation of spike-like “dendrites” which can grow long enough to puncture the battery separator causing the battery to short circuit. | The likelihood of lithium plating grows when charging at low temperatures (lowering the rate at which the anode and cathode can accept lithium ions) and fast charging (increasing the rate of arrival of ions at the anode). Keeping batteries above 15°C (59°F) and minimizing fast charging reduces risk. |
Mechanical Stress The process of repeatedly accepting and releasing lithium ions as the battery is charged and discharged places a stress on the molecular structure of the cathode, anode and SEI layer. Over time this strain can cause permanent changes in these structures, lowering the capacity and rate of lithium-ion storage. | Fully charging / discharging the battery puts additional strain on the battery by increasing the volume of lithium ions the anode and cathode accept and release. Fast charging also increases strain by accelerating the rate at which the anode has to accept lithium ions. Keeping the battery's state of charge in the 20-80% range, reducing the frequency of full charge/discharge and minimizing fast charging lowers risk. |
Cathode Dissolution Time and battery use can yield reactions within the electrolyte that raise its acidity and cause it to dissolve the cathode material. The damaged cathode is less capable of holding lithium ions. Additionally, the dissolved cathode material can travel through the electrolyte to accelerate SEI layer growth and lithium plating. | Storing and using batteries at high voltage and temperature can accelerate cathode dissolution. Batteries should be kept below 35°C (95°F) and 80% SOC whenever possible to lower risk. |
Note: Fast charging can cause battery temperatures to rise above the 35°C (95°F) threshold, triggering accelerated aging via SEI layer growth and cathode dissolution. This happens because the materials used to conduct electricity in the battery are not 100% efficient, so during charging some of the electrical energy is lost to heat. Thus, higher charging speeds yield more heat generation. If the heat generation exceeds the battery management system’s ability to cool the battery, it will start to heat up.
When should ESB batteries be replaced?
ESB batteries should be replaced when their capacity significantly reduces such that the drivers can no longer serve their original routes. However, because school bus routes and battery aging profiles vary so broadly, this exact point will differ case by case. Older ESBs can be moved to lower mileage routes to extend their lifetime, and when the battery is no longer fit for the vehicle, there are several ways they can be sustainably managed. Historically, when LIBs have experienced a certain level of aging, a large percentage of them encountered a “knee point” where the rate of capacity loss accelerates abruptly. Knee points are often the result of self-reinforcing aging mechanisms that can result in rapid degradation and shortened battery life. To avoid unforeseen incidents, ESB manufacturers typically recommend replacing the battery when it drops to about 70% of original capacity.
Early indications from electric cars suggest vehicle batteries may last longer than initially expected. This 2020 analysis from Geotab across 21 electric vehicle models shows an average of 12% battery capacity loss over 6 years.
What impact does Vehicle to Everything (V2X) use have on aging?
V2X is an all-encompassing energy technology concept in which an electric vehicle is viewed as a mobile battery, and stored energy in the vehicle can be discharged for some benefit (e.g. sending power to an electric grid or building). Because V2X activities may increase the number or frequency of charge and discharge cycles in a battery, they could accelerate battery aging. School districts should inquire with their dealers/OEMs about expected impacts from V2X services on their ESB battery. V2X pilots using ESBs and other vehicle types are underway nationwide and may shed light on the impacts of V2X services on battery aging.
What is the battery industry doing to slow aging?
There has been significant industry focus on curtailing aging by developing more advanced thermal management systems. Improvements have also been made with respect to ESB batteries’ ability to withstand high speed charging, with limited recent data suggesting that certain light-duty vehicle batteries may be able to withstand frequent fast charging without accelerating capacity loss. These improvements have happened while maintaining an excellent safety record: a recent report from the Swedish government’s Authority for Social Protection and Preparedness found that EVs were 29 times less likely to catch fire than internal combustion engine vehicles. Here’s more about electric school bus battery safety.
Tweaking cathode and anode materials, cell and pack designs, and manufacturing methods should continue to produce incremental improvements in aging for traditional LIBs. However, researchers are also investigating alternatives to traditional LIBs, like sodium-ion and solid-state batteries, which could yield drastic improvements.
How do ESB battery warranties account for aging?
ESB warranties account for the effects of aging by covering batteries through (the lesser of) certain time (in years) and use (in total miles and / or kWh of power throughput) limits. These limits typically give ample time for ESB owners to identify and replace faulty batteries during the warranty period, which is important given the high cost of replacement (batteries account for ~40% of total ESB cost).